—It started in Memphis, Tennessee with a crafty father who liked to work with leather. Now, brothers Chris and Kirk Bray are the founders of the bespoke Jersey City-based brand, Billykirk.
The Birth of a Brand
When Chris and Kirk Bray first picked up their father’s knife scabbard decades ago, a part of them always knew leather would fill their lives. Inside their family studio, the two captivated teens developed a mutual admiration not just for the finished product, but its journey from the cattle to a functional utilitarian tool.
“We were at an impressionable age,” Chris told me, during my visit to their Jersey City studio earlier this spring. “Kirk and I fell in love with how pliable and workable leather was. When you wrap wet leather around something and hold it into place, it’s going to stay like that. Then you start to work with the leather; it darkens and takes on a patina. You begin to really see the leather and how it changes—how it ages. The simple idea of working with our hands attracted both Kirk and I.”
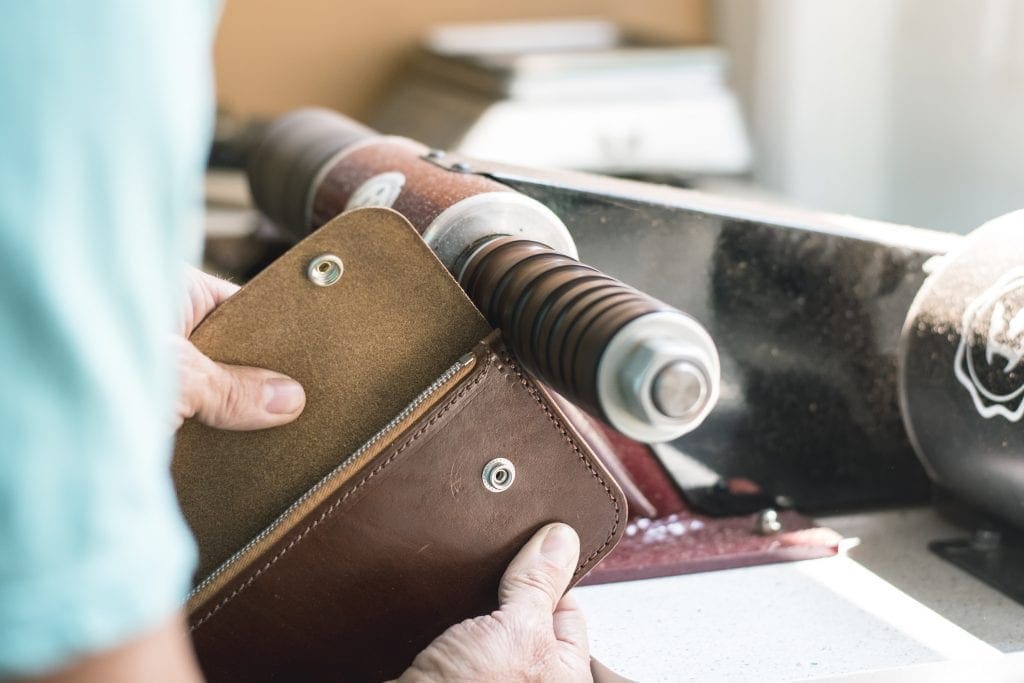
BIllykirk Large Trucker Wallet
The two brothers grew up in a creative family. Their mother was an interior designer and lover of fine arts. Their father spent years as a prop master at a local theater and would often lose himself in hobbies such as woodcarving, knifemaking and stained glass. During their adolescent years, the family uprooted from their Tennessee home to relocate to Minnesota. Later in college, Chris studied acting and Kirk received an Apparel Design degree. It wasn’t long before their career paths naturally landed them in West Los Angeles. But like many who venture to the West Coast in search of professional glory, they soon found themselves devoting their time to dead-end jobs.
“I was still trying to become an actor. I had people covering for me at my nine-to-five so I would have to speed out to auditions,” Chris explained. “It wasn’t conducive. I did college films, took acting classes, even did some daytime TV. Finally, I read a statistic that said that only three percent of Screen Actor Guild members made over $80,000. That certainly took the wind out of my sails. I knew it wasn’t the career path for me. My heart wasn’t in it anymore.”
Things simply felt out of place for the Brays. Despite this, the two brothers never abandoned their love of craft. On their days off, they visited thrift stores, pawnshops and began selling their vintage finds on eBay. Their affinity for “old stuff” turned into a small collecting business. That’s also when they found their catalyst: an old leather watch strap inside a pawnshop in Santa Monica, CA. The Brays didn’t know it yet, but that piece of leather would soon be the jumping-off point for their very own brand.
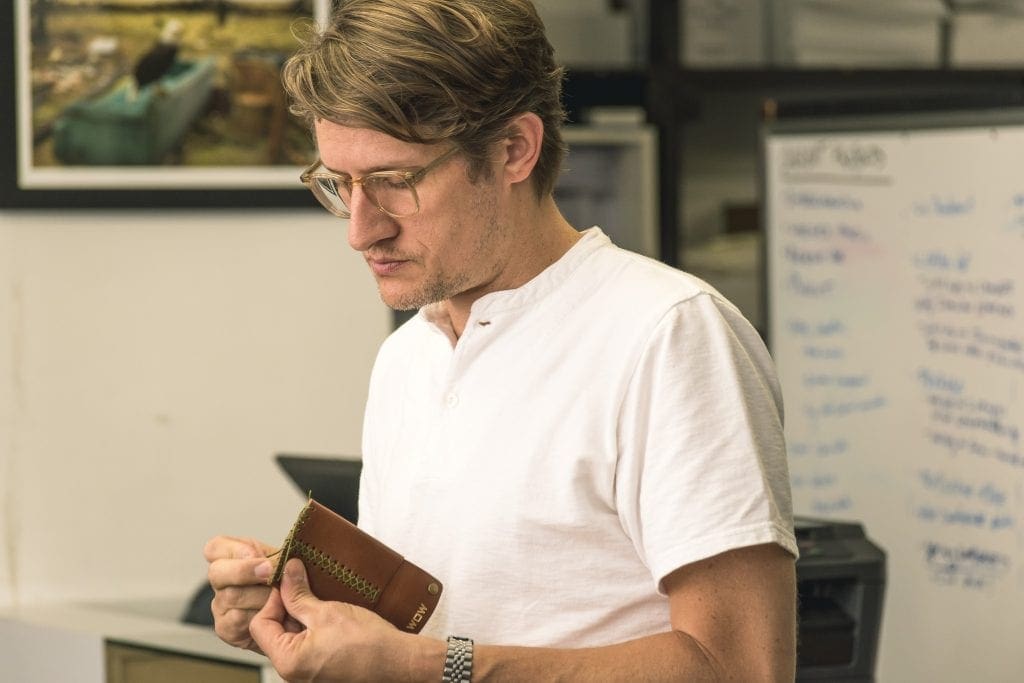
Co-founder of Billykirk, Kirk Bray
“Kirk was able to persuade this guy into selling us just the strap without the watch. He would wear the strap at the coffee shop he was working at. Everyone thought it was really cool. Soon we thought, ‘Hey, we can make these.’ So one day I picked up the Yellow Pages and I looked for wholesale leather. There was a place called Caldelle Leather just three miles away in Santa Monica. They gave us a big tutorial on what kind of leather to buy, what cutting supplies we needed and where to get hardware.
From there, we started to hand-make cuffs and watchstraps. In 1999, we started thinking about doing a tradeshow and coming up with a brand which we named after Kirk (William Kirkland)—everyone in the family would call him Billy Kirk. We just liked the name. It’s also an homage to our father and our Southern roots where you meld the first and middle names together.”
By 2005, despite Billykirk’s success, the Brays had enough of California. Call it the lack of seasons. Or, maybe, call it the abundance of traffic on the 10 freeway. It was time for a change. And so they decided to pick up and move their brand (and two households) to New York—their fourth city (and now fourth accent).
A Culture of Craft
Kirk and I are standing around Billykirk’s 1930s cutting table, where he’s teaching me to stitch my own card case. I finish and head over to Chris’s station where he pulls down on a vintage heat stamp machine, embossing my initials “M.S.” into the bottom corner of my new card case while I sip on an old fashioned. It’s 2019, and there’s just something about whiskey and leather.
Fast-forward to today. The Brays have moved their 150 Bay St. studio in Jersey City down a few floors to a larger space that will soon have retail and room for events and workshops. I’m back at the same wooden cutting table leaning on one of its cast-iron corners. Kick press machines from the early 1900s and old leather items from the U.S. Military are scattered along the edges of the room. Like everything Billykirk makes, these inspiration pieces were made to last by craftsmen who came before them—a true counter to mass production. Each antique ignites their passion. It’s akin to the allure of two kids holding their father’s scabbard while growing up in the South and Midwest.
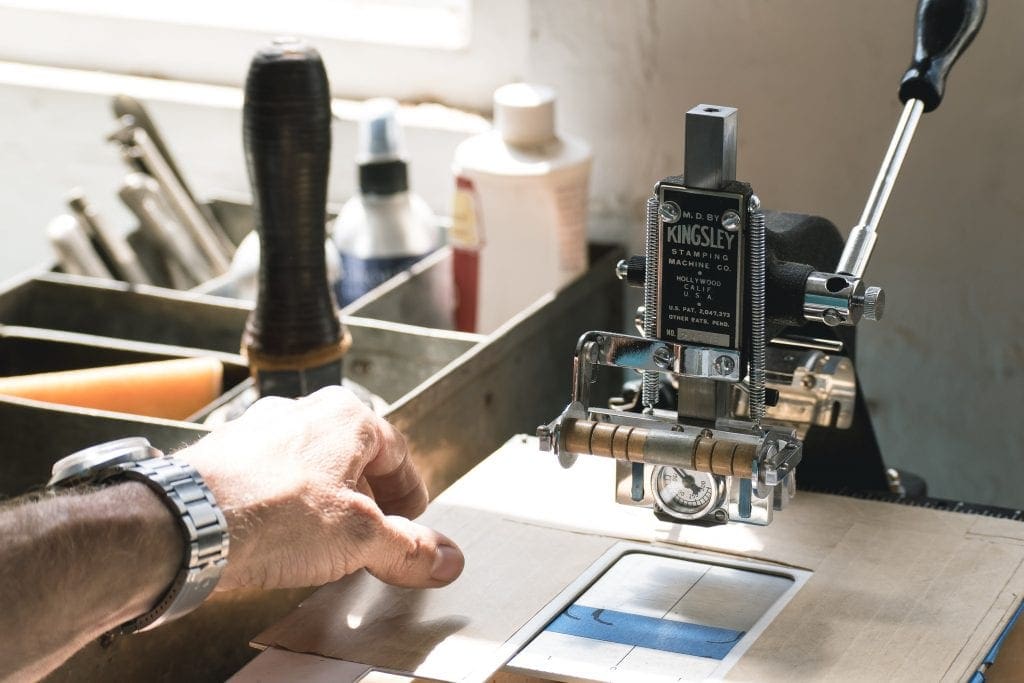
Kinglsey kick press machine at Billykirk studio
“From our standpoint, most mass-produced items today are simply future landfill clutter,” Chris said. “When we developed this company, we had this idea to make something that you want to pass down. You look at companies like Filson or Russell Moccasin, these weren’t fashionable brands by any stretch of the imagination in the 1990s. They were both hard-working, outdoor brands made with quality materials that our father would hunt with.”
“These brands are both full of classic designs that are made well,” Chris continued. “There are no bells and whistles. They’re not trendy, and that’s what we want Billykirk to be. Products that are made well, that you will pass down—that you will want to use because they’re timeless and have a soul. When that happens, the item not only becomes relied upon and appreciated but also, revered. Someone will call us every so often and say, ‘My wallet was stolen. I don’t care what was inside, I had that wallet for 15 years.’ It really means something to them. There’s a lot of travel and memories behind these humble objects.”
Even with something as simple as a wallet, it’s surprising how much goes into the creation process. For Billykirk, that journey starts at the source. Sourcing is a never-ending mission to find the right domestic leather. When the brothers first began on the West Coast, they would source much of their material from a renowned tannery called Salz in Santa Cruz, CA. When the family decided to cash in on a land sale, Salz was no more.
“Since Salz closed, we’ve been hunting for these recipes,” Chris explained. “A lot of companies have tried to mimic what Salz did but have not quite hit it. We’ve gone through a lot of [good] tanneries. Your belt leather is different from your bag leather. You need some continuity. If you have a bag that’s soft leather, the strap is going to be harder or rigid. You’re always hoping these tanneries develop new samples (and thankfully they have).”
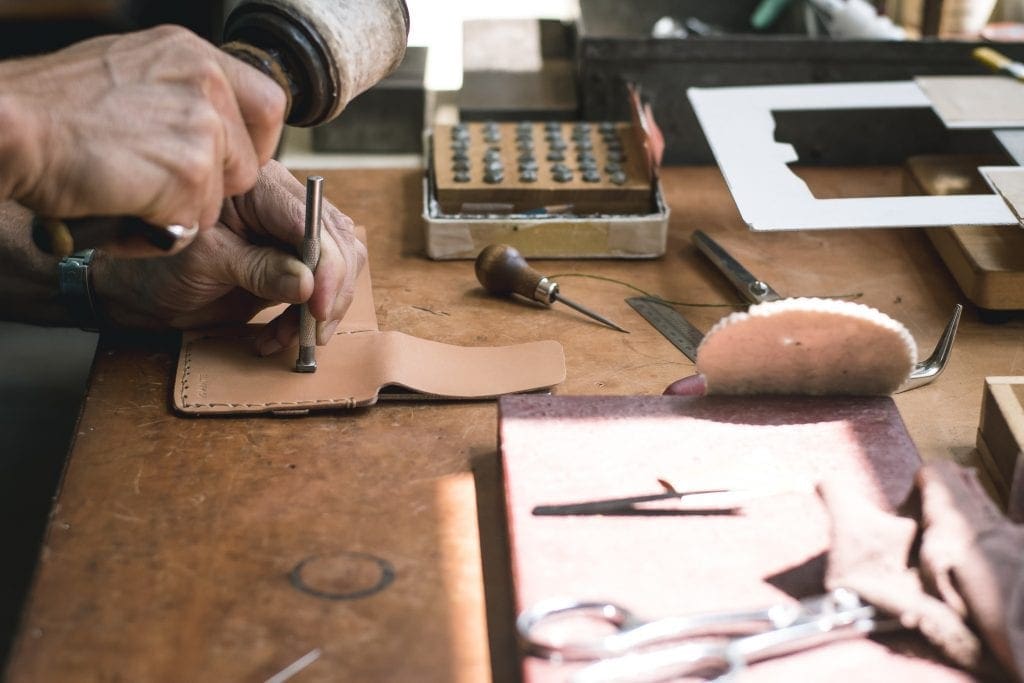
Leather edge beveler
Each hide of leather that arrives from a tannery has to be blocked out before it can become anything—heavyweight leather is stripped for belts, thinner leather for small accessories. Then comes the skiving, beveling, edging, and hand-stitching. The Brays don’t dye any leather they receive, preferring the natural colors that result from the tanning process. From tanneries like Horween in Chicago—who was the official supplier of the U.S. Marine Corps in the 1940s—to Billykirk’s Jersey City studio, the journey of each piece evokes a certain nostalgia. The old-world tanner-leatherworker relationship is reminiscent of artisans from centuries past, a call back to the early 1900s when craft guilds held a prominent place in the neighborhood.
“These were people that were really highly respected in the community,” Chris explained. “In New York, you just have to look up at all the beautiful mosaic work to touch on that history. Certain immigrants were skilled at certain crafts. The Italians were involved in a lot of the intricate carvings on the facades of buildings. The Irish also helped build New York. It’s said that so many Irish were killed working on the railroad that it was commonly speculated that ‘there was an Irishman buried under every tie.’”
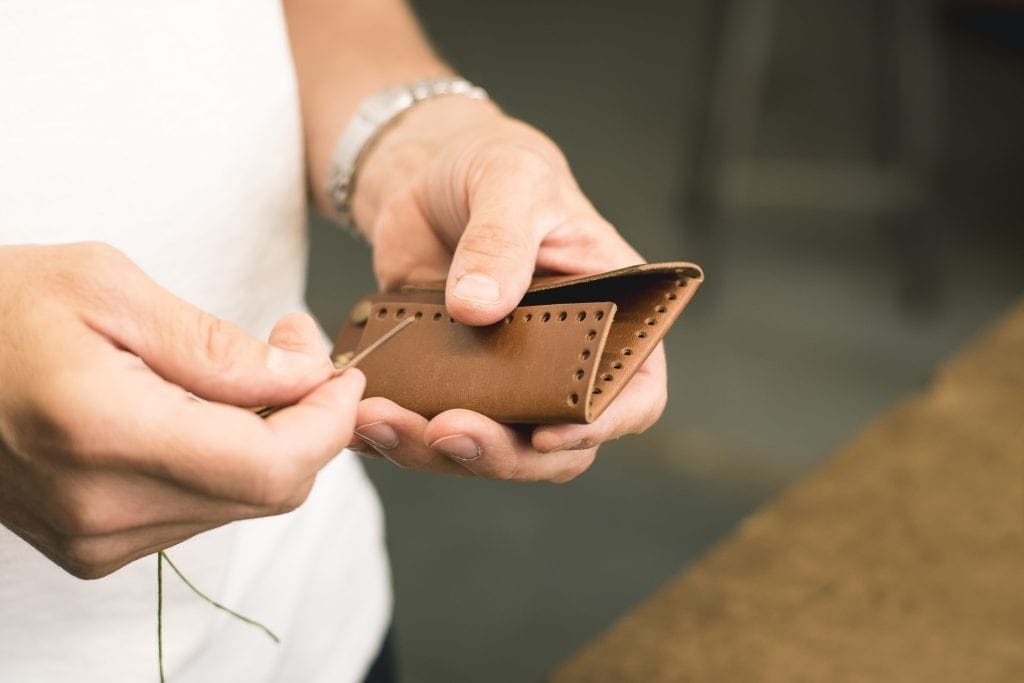
Hand stitching Billykirk accessories
“Crafts were an important part of living. Today, people want to get things done quicker. Unfortunately, it comes down to greed and who your shareholders are. Billykirk is not beholden to anybody. We don’t have to have our stuff made outside the country. We’re small-batch, bespoke in our own way.”
An Answer to Fast Fashion
In the 1990s, the term “fast fashion” became fierce in the industry. Droves of cheap garments marched off from the catwalks and stormed retail locations everywhere—all to stay on-trend. After the 2008 recession, professionals on Wall Street pivoted to the garment industry because they had a taste for fashion and their jobs were gone. The concept of fast fashion was exacerbated further.
“A lot of companies sprang up out of [2008] that weren’t created by fashion people,” Chris said. “They had deep pockets and could afford to hire smart people to develop a line. I believe people are now getting tired of fast fashion. They want to start buying things that, after five years, aren’t falling apart or losing their structure. If you’ve ever had a nice suit, you know immediately when you put it on—especially if it’s made to fit you. There’s nice lining, double stitching, good buttonholes—it drapes perfectly. The same goes for one of our bags or belts—it’s going to wear in and be with you for years because it’s made with good ingredients and made properly. It’s not going to fall out of trend because it isn’t trendy. You could use a Billykirk item in 20 years and you’re not going to think it’s dated.”
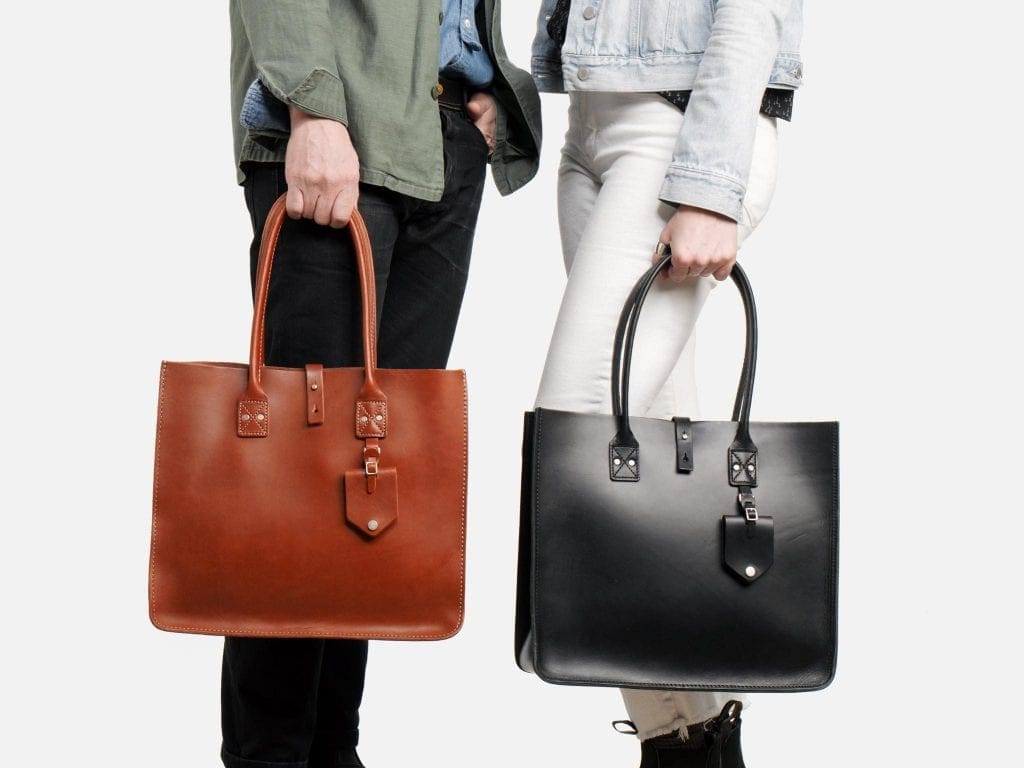
Tan and black leather totes from Billykirk
Billykirk’s anti-trend approach to products led to web sales becoming the bulk of their business—bags, belts, valet trays. In recent years, Chris and Kirk have expanded to offer creative design services–one that brands, hotels, restaurants and design houses can contract for interior design elements, custom gift shop items, and corporate gifting. For a brand like Billykirk, though, whether it’s a collaborator or influencer, there has to be a good connection. The brand, the DNA—everything has to fit.
“Kirk and I have been doing collaborations for brands like Vans Vault, Levi’s, Hudson’s Bay Co., Cole Haan, and J. Crew for years,” Chris explained. “We’ve had a blast working with all of these super creative development teams. In the last 10 years, we’ve also become a creative design service for a lot of industries. We’re currently making stationary wall pockets for a new Ace Hotel in Toronto and looking forward to making more leather all-access passes and band merch when all the bands we work with get back on the road. We also recently developed nautical-inspired ‘Do Not Disturb’ signs that were two-sided leather and foiled stamped for The Lake House [in Canandaigua, NY]. We’re focused on pieces that are super unique and reflect the ethos of the companies we are working with.”
In an effort to stay sustainable in the foreseeable future, Chris and Kirk are also devoted to developing some plant-based materials to work with. “There’s mushroom leather, giant leaf leather that people have been working with,” Chris told me. “We’re trying to create something for people who don’t want to use leather. My wife and I haven’t eaten meat for a number of years. We’re getting there. We recognize that’s an important thing. We’re aiming to launch a vegan leather that feels good. There have been leather-like materials over the years but they are often just petroleum-based garbage.”
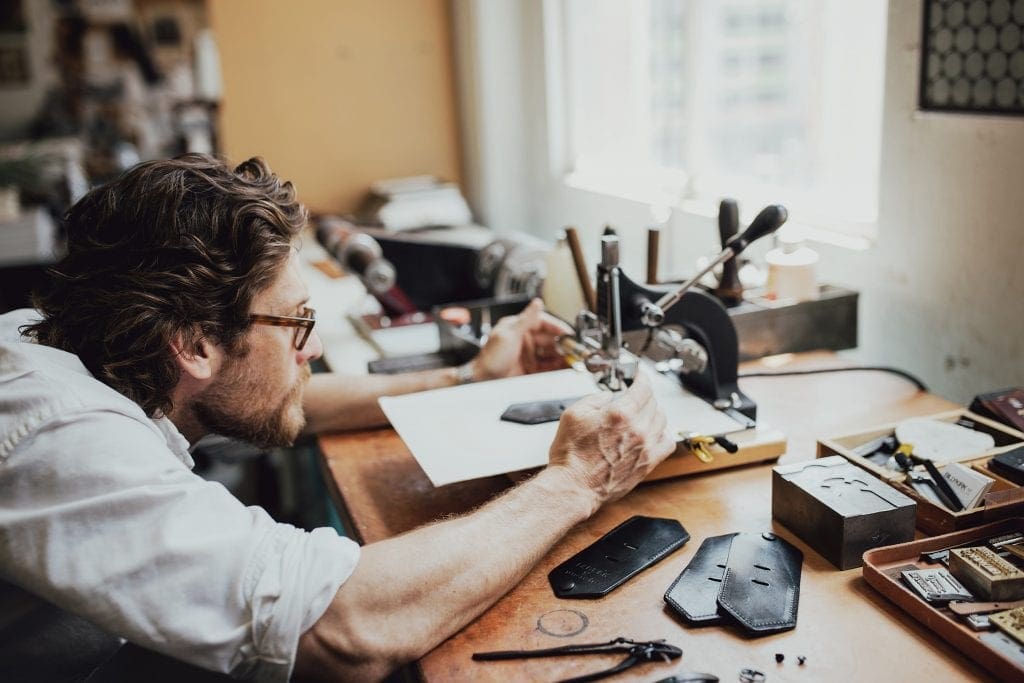
Co-founder of Billykirk, Chris Bray
If you ask Chris and Kirk where they’re from, you’ll get a few different answers. Influences of the South, Midwest, West Coast and now, the Northeast, work in unison to shape their leather goods. For the Bray brothers, their journey from their father’s workshop to their Jersey City studio is one as magnetic as the hand-sewn wallets and natural waxed totes they create. What began with a simple knife scabbard and an inch-and-a-quarter-wide watch strap has become a brand they can be proud of. With each passing year, their story and the character each Billykirk piece embodies grows louder with the changing of seasons. Every time a belt is taken off, every time a tool bag is opened—it’s building the next part of the story—the soul of the leather.
“These pieces become part of their owner. The journey doesn’t end when you buy it. I think we were definitely at the forefront of this ‘Made in America’ resurgence. But we were making it in the U.S. because we’ve always been here. It wasn’t because we wanted to be known for being a ‘Made in America’ company. It’s just a vital part of who we are.”
Photography by Tatsuro Nishimura (@tatsuro_nishimura), Ray Spears (@rayneutron,) Whiskey & Oxfords (@whiskeyandoxfords)
About the Author/s
Michael is the Editor-in-Chief of New Jersey Digest, COO of X Factor Media, and an avid writer. Growing up in Bergen County, he discovered his passion for words while in Friday detention. Michael loves kayaking, a fat glass of Nebbiolo, and over-editing.